Ang mga overhead crane ay gumaganap ng isang mahalagang papel sa iba't ibang mga industriya, na nagsusulong ng mahusay na paghawak ng materyal at pinapasimple ang mga operasyon. Gayunpaman, pagkatapos ng mahabang panahon at mataas na dalas ng paggamit, na apektado ng mga salik tulad ng labis na pagkarga, ang mga bridge crane ay madaling kapitan ng mga pagkabigo sa pagpapatakbo, na kung saan ay nabigong gumana nang maayos at nagdudulot ng ilang mga abala sa industriyal na produksyon. Samakatuwid, kinakailangang pag-aralan ang mga piyesa, pagkabigo ng controller, pagkabigo ng preno, pagkabigo ng reducer, pagkabigo ng kuryente at iba pang karaniwang mga pagkakamali, kolektahin ang kaukulang mga ekstrang bahagi, at gumawa ng mga naka-target na hakbang upang harapin at ayusin upang matiyak na ang bridge crane ay maaaring tumakbo. maayos.
1. Mga Fault ng Hook
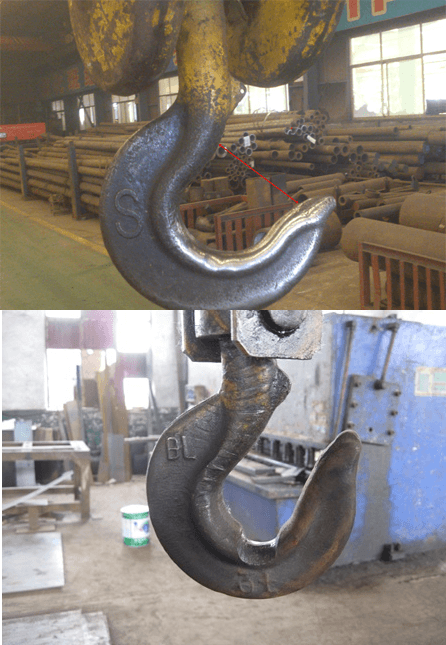
- Mga Bitak sa Pagkapagod: Maaaring lumitaw ang mga bitak sa pagkapagod sa ibabaw ng kawit dahil sa madalas na overloading at labis na stress habang ginagamit. Ang mga depekto sa materyal at mahinang kalidad ay maaari ding maging sanhi ng pagkasira o pagkasira ng kawit, na humahantong sa mga aksidente.
- Pagbukas at Mapanganib na Pagsuot ng Seksyon: Dahil sa madalas na paggamit, ang crane hook ay madaling kapitan ng mga problema tulad ng pagtaas ng pagbukas at pagkasira sa mapanganib na seksyon. Ang paggalaw at alitan ng wire rope ay maaaring lumikha ng mga grooves sa hook. Kapag ang pagbubukas ng hook ay lumampas sa 15% ng orihinal nitong laki o ang mapanganib na pagkasuot ng seksyon ay umabot sa 10% ng orihinal nitong sukat, ito ay nagpapahina sa lakas ng hook at maaaring magdulot ng deformation o detachment, na magreresulta sa mga aksidente.
- Plastic Deformation: Ang matagal na overloading o pagkakalantad sa high-temperature radiation ay maaaring magdulot ng plastic deformation sa pagbubukas at baluktot na mga bahagi ng hook, na maaaring magresulta sa pagkakatanggal ng mabibigat na bagay at aksidente.
Pag-troubleshoot ng Overhead Crane Hook
- Sa kaso ng pagkapagod na mga bitak sa kawit, dapat itong palitan kaagad.
- Ayon sa mga regulasyon sa pag-scrap para sa mga kawit, dapat itong i-scrap kung ang pagbubukas ay lumampas sa 15% ng orihinal nitong laki o ang mapanganib na pagsusuot ng seksyon ay umabot sa 10% ng orihinal nitong laki. Kung hindi ito lalampas sa mga pamantayan, maaari itong patuloy na gamitin sa ilalim ng pagmamasid o may pinababang pagkarga, ngunit hindi pinahihintulutan na gamitin ang welding rod upang ayusin at pagkatapos ay gamitin muli.
- Sa kaso ng plastic deformation na nagaganap sa pagbubukas at baluktot na mga bahagi ng kawit, dapat itong palitan. Sa mataas na temperatura o metallurgical operating environment, kapag ang temperatura ng thermal radiation ay lumampas sa 300 degrees, ang isang radiation shielding plate ay maaaring welded upang ihiwalay ang heat radiation at protektahan ang hook.
2. Wire Rope Faults
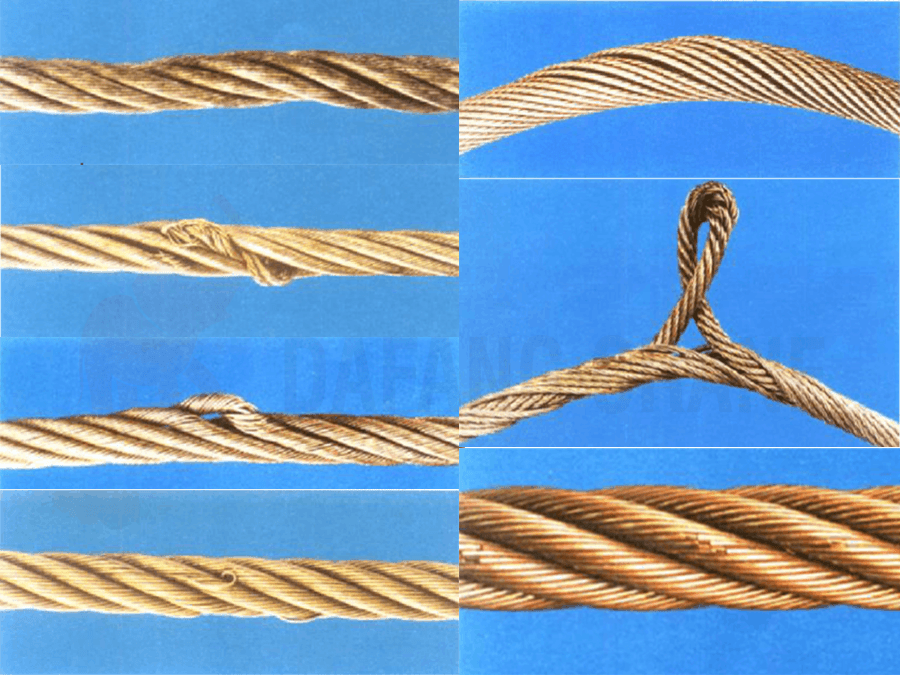
- Pag-twisting: Sa ilalim ng normal na mga kondisyon sa pagtatrabaho, ang mga wire rope sa magkabilang panig ng movable pulley group ay dapat na parallel at hindi nakakasagabal. Gayunpaman, kapag ang wire rope ay "twist," ang mga lubid sa magkabilang panig ng movable pulley group ay tumatawid sa isa't isa sa isang "figure eight" o "twisted" na hugis. Ang hindi pangkaraniwang bagay na ito ay nangyayari bilang resulta ng panloob na konsentrasyon ng stress na dulot ng pag-install o pagpapalit ng mga bagong wire rope sa paglipas ng panahon.
- Random Rope Twisting on the Reel: Kapag nangyari ang sitwasyong ito, ito ay sanhi ng pagkabigo sa rope guide. Ang rope guide ay naka-install sa reel at ang tungkulin nito ay upang matiyak ang makinis na pag-unwinding at paikot-ikot ng wire rope mula sa reel at upang maiwasan ang tali mula sa pagkakabuhol-buhol sa panahon ng proseso.
- Pagkapagod ng Wire Rope: Ang mga abnormal na pangyayari tulad ng mga sirang wire, sirang mga hibla, kaagnasan, pagpapapangit, at pagkasira ay lumilitaw sa ibabaw ng wire rope. Sa panahon ng normal na paggamit, ang wire rope ay napapailalim sa mga panlabas na puwersa tulad ng friction, impact, at compression, na nagreresulta sa pagkasira ng wire rope.
- Kinking: Ang permanenteng deformation ng wire rope na dulot ng local twisting ay tinatawag na kinking. Kung ang dulo ng wire rope strand ay hindi nakatali kapag ang tensyon ay inilapat, ang strand ay iikot sa tapat na direksyon, na kung saan ay ang likas na kadahilanan na nagiging sanhi ng kinking ng wire rope.
Pag-troubleshoot ng Wire Rope
- Kapag nag-i-install o nagpapalit ng mga wire rope, dapat bigyang pansin ang pagpili ng mga lubid na may mahusay na anti-kinking performance at pagtutugma ng rope twist direction sa winch drum. Gamitin ang tamang rope threading technique upang maiwasan ang pagbuo ng twisting stress sa panahon ng proseso ng threading. Kung sakaling umikot ang wire rope sa panahon ng operasyon, dapat na pansamantalang suspendihin ang lifting task, at may wastong pag-iingat sa kaligtasan, bitawan ang panloob na stress ng wire rope sa pamamagitan ng pag-alis ng hugis-wedge na dulo, pagkatapos ay muling i-install at i-secure ang hugis-wedge na ulo. Bago ipagpatuloy ang operasyon, magsagawa ng lifting test upang kumpirmahin na ang problema ng wire rope twisting ay nalutas.
- Ang rope guide ay isang vulnerable component, at kapag ito ay malubha na, ito ay mabibigo sa paggabay sa lubid ng maayos, na nagreresulta sa rope entanglement, dapat itong palitan ang rope guide sa oras na ito. Sa tilted lifting operations, ang rope guide ay mas madaling masuot, kaya sa production, ang lifted load ay dapat panatilihing patayo sa electric hoist.
- Sa araw-araw na operasyon ng crane, palakasin ang pagsubaybay sa kondisyon ng wire rope at hatulan ang katayuan ng paggamit nito. Kapag naabot na nito ang nauugnay na pamantayan sa pag-scrap, palitan kaagad ang wire rope na nakakatugon sa pamantayan sa pag-scrap.
- Ang paglutas ng mga fault ng wire rope ay maaaring mangailangan ng mga bahagi tulad ng wire rope at rope guides.
3. Mga Fault ng Controller
Kasama sa mga karaniwang pagkakamali ng controller ang mahinang contact at hindi isinasara ang contact. Ang mga sanhi ng mga problemang ito ay matinding oksihenasyon ng contact contact surface, hindi pantay na contact surface, maluwag o pagod na mekanismo ng controller. Ang mga nasirang remote controller ay karaniwan ding mga pagkabigo.
Ang pag-troubleshoot ng controller ay dapat palaging suriin ang kondisyon ng contact, higpitan ang maluwag na fixing bolts, palitan ang mga nasirang bahagi sa oras, at magdagdag ng lubrication sa mga umiikot na bahagi.
4. Mga Fault ng Preno
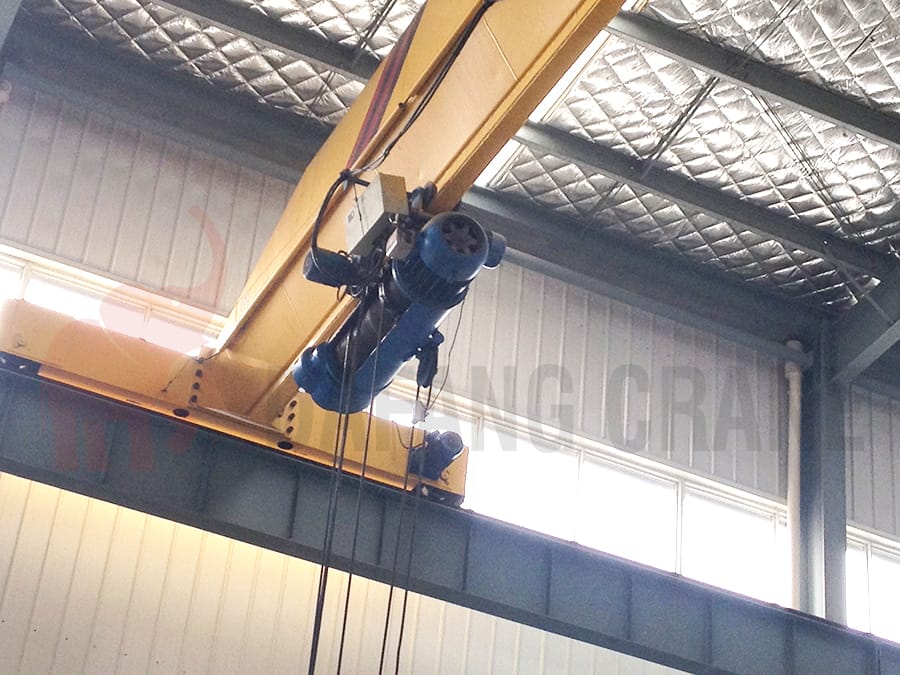
- Brake Failure: Ang brake failure ay ipinahihiwatig ng sobrang sliding distance habang nagpepreno, karaniwang lumalampas sa 80 mm.
- Kawalan ng Kakayahang Bitawan ang Preno: Kabilang sa mga pangunahing dahilan ang pagkaka-jam ng hinge point at mahirap i-rotate nang normal, ang pagkakaroon ng hangin o kakulangan ng langis sa hydraulic solenoid at hydraulic push rod cylinder, sobrang elastic na main spring, dumi sa brake pad, at mataas na boltahe na humahantong sa pagka-burnout ng mga rectifying coils at mga bahagi, pati na rin ang mga fault sa electromechanical device circuit.
- Patuloy na Pagbaba ng Brake Torque: Pangunahing sanhi ito ng pagkasira ng brake pad, matinding pagkasira ng butas ng hinge point sa frame ng preno, at patuloy na pagpapahinga ng pangunahing spring.
- Pag-init ng Brake: Pantulong na pinsala sa tagsibol o pagyuko sa mga short-stroke na preno, at magaspang na gumaganang ibabaw ng gulong ng preno. Maling clearance sa pagitan ng brake pad at ng brake wheel.
Mga Partikular na Panukala sa Pagpapanatili ng Preno
- Ang pagkabigo ng preno ay maaaring dahil sa labis na clearance sa preno, ang pagkakaroon ng kontaminasyon ng langis sa ibabaw ng friction, o labis na pagkasira ng friction surface. Ang naaangkop na clearance ay maaaring makamit sa pamamagitan ng bahagyang paghihigpit ng nut. Kung ang pressure spring ay pagod na, dapat itong palitan. Kung ang brake ring ay malubhang nasira at hindi matiyak ang isang makatwirang braking clearance, ang brake ring ay dapat palitan. Kapag pinapalitan ang brake ring, alisin muna ang brake wheel, tanggalin ang orihinal na brake ring, bahagyang lagyan ng tubig ang bagong brake ring rubber ring, at i-embed ito ng maayos.
- Tanggalin ang jamming at mag-lubricate; lumikas ng hangin at magdagdag ng langis; ayusin ang pangunahing puwersa ng tagsibol; regular na linisin ang gulong ng preno sa loob ng bridge crane, mas mainam na gumamit ng kerosene para sa paglilinis, at mag-lubricate ang brake pad sa loob; palitan ang mga nasunog na electromagnetic coils at mga bahagi; suriin ang electrical circuit.
- Napapanahong palitan ang mga brake pad ng pagkasuot na lampas sa 50% ng orihinal na kapal at palitan ang mga pin ng pagkasira na higit sa 5%, gamit ang mga pamamaraan tulad ng reaming at pag-install ng mga bagong pin upang maalis ang pagkasira sa mga butas.
- Palitan o ayusin ang mga auxiliary spring; makina ang gumaganang ibabaw ng gulong ng preno kung kinakailangan; ayusin ang clearance.
- Ang paglutas ng mga pagkabigo sa preno ay maaaring mangailangan ng mga bahagi tulad ng mga pressure spring, pangunahing bukal, pantulong na bukal, maliliit na baras, gitnang baras, brake ring, friction pad, at iba pang bahagi.
5. Reducer Faults
- Paglabas ng langis: Ang pagtagas ng langis ay nangyayari kapag ang ibabaw ng reducer ay hindi makinis, at ang lubricant ay nawawala ang bisa nito. Ang hindi pantay na sealing coating o nasira na sealing gasket sa sealing surface, pati na rin ang deformation ng casing o loosening ng connecting bolts, ay maaari ding maging sanhi ng oil leakage.
- Pagkasira ng gear: Sa panahon ng operasyon, ang mga gear ay maaaring makaranas ng bali at pagkasira. Ang kaagnasan ay maaari ding mangyari sa panahon ng operasyon.
- Shaft fracture: Ang shaft fracture ay nangyayari kapag ang reducer shaft ay sumasailalim sa mga puwersa ng baluktot at pagkasira.
Mga Panukala sa Pagpapanatili para sa Reducer Equipment
- Ayusin ang flatness ng mga bahagi ng reducer upang matugunan ang mga kinakailangan; palitan ang mga seal; ayusin ang pambalot, at palitan ito kung malubha ang pagpapapangit; higpitan ang mga bolts.
- Palitan ang mga bearings.
- Palitan ang mga gears.
- Ang paglutas ng mga pagkabigo sa reducer ay maaaring mangailangan ng paggamit ng mga bahagi tulad ng mga gear, bearings, sealing gasket, at sealing box.
6. Mga Fault ng Electrical System
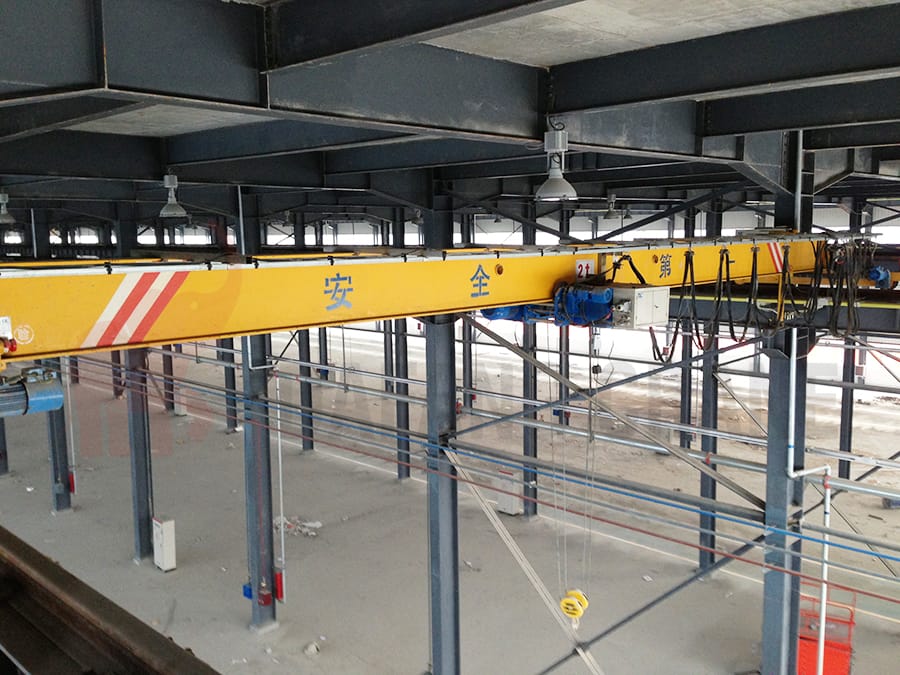
- Kabiguan ng motor: Ang metalikang kuwintas ng pagsisimula ng motor ay maliit, hindi maaaring magsimula, abnormal na tunog.
- Isolated conductor rail failure: Ang pangunahing power supply system failure ay pangunahing power supply isolated conductor rail failure. Tulad ng mga power failure na dulot ng nakahiwalay na conductor rail, ang halatang deformation ng conduit na dulot ng collector ay hindi magagalaw, brush side abrasion at ang ibabaw ng granular pit, ang wobble ng conduit ay masyadong malaki sa panahon ng trabaho, brush wear too mabilis, dumudulas ang device na may malaking tunog at mga abrasion ng shell. Ang dahilan ay madalas ang pagpapapangit na dulot ng hindi naaangkop na pag-install ng guide rail, ang ambient temperature ay masyadong mataas na thermal expansion na dulot ng jamming, ang kolektor ng maling pag-install at paglihis sa pagpoposisyon, atbp.
- AC contactor failure: Overhead crane sa operasyon dahil sa contactor point at madalas na isinasara ang aksyon, kaya madaling contactor coil burning at sirang wire failure, dahil sa coil fixing bolt loosening, contactor rotating mechanism shifting leads to the movable and static iron core higop misalignment, ang core higop na may hawak na kasalukuyang pagtaas; gumawa ng auxiliary contact mahinang contact, ang boltahe ng coil sa magkabilang dulo ng coil ay nabawasan. Nagdulot ng pagkabigo ng coil; Ang contactor dynamic at static na mga contact ay sinusunog o at sinusunog ng arc.
- Resistor pangunahing faults: Resistive sirang wire, ay hahantong sa rotor open circuit; resistive pinagbabatayan, na nagreresulta sa rotor kasalukuyang kawalan ng timbang, malubhang rotor winding malubhang init; resistive connecting terminal init.
Mga Panukala sa Pagpapanatili ng Electrical System
- Suriin kung normal ang three-phase power supply ng motor sa metro ng electrician, kung mayroong undervoltage, phase shortage, atbp., kung normal ang motor collector ring, carbon brush at wire, kung ang insulation resistance ng motor ay normal. qualified man o hindi, at ang motor shaft o bearing ay pagod o nasira ay magdudulot din ng fault na ito. Suriin upang matukoy ang sanhi ng kaukulang pagpapanatili o pagpapalit ng mga nasirang bahagi.
- Palakasin ang inspeksyon ng mga masusugatan na bahagi ng power supply sliding isolated conductor rail system, napapanahong pag-aayos o regular na pagpapalit ng kolektor. Pana-panahon o madalas na suriin ang kondisyon ng nakahiwalay na gabay sa riles ng konduktor at ayusin ang sliding hanger upang malayang lumawak ang conduit. Palakihin ang seksyon ng thermal expansion ng conduit, magdagdag ng mga shade at gumamit ng mga heat shield sa labas.
- Regular na magsagawa ng komprehensibong inspeksyon at pagpapanatili ng mga de-koryenteng bahagi sa power cabinet. Suriin ang mga wiring ng coil at ang mga nakapirming bolts para sa pagkaluwag, at alisin agad ang mga depekto; higpitan ang mga maluwag na contact at palitan ang mga nasirang contact sa oras. At gawin ang isang mahusay na trabaho ng contactor contact pagsasara sa panahon ng parehong panahon ng inspeksyon, pagsasaayos ng trabaho.
- Regular na suriin ang risistor kung may mga hot spot at sirang wire, higpitan ang connecting bolts, at regular na suriin ang insulation resistance ng rotor at risistor at kung balanse ang three-phase rotor current.
- Ang pag-troubleshoot ng electrical system ay maaaring gumamit ng mga bahagi tulad ng mga collector, cable, bearings, at contactor.
Pagkatapos ng mahabang panahon ng paggamit, ang ilang bahagi ng bridge crane ay hindi maiiwasang masira, mapunit upang maabot ang end-of-life standards kailangang palitan ng mga bagong piyesa upang maiwasan ang mga aksidente. Ang mga karaniwang pagkabigo ng mga overhead crane ay kinabibilangan ng mga component fault, controller faults, brake faults, reducer faults, electrical faults at iba pa. Ang mga bahagi na maaaring magamit upang malutas ang mga pagkakamali ay:
- Component fault: wire ropes, rope guides, hooks, pulleys, wheels, reels
- Kasalanan ng controller: remote control
- Fault ng preno: pressure spring, main spring, auxiliary spring, maliit na shaft, mandrel, brake ring, brake wheel, friction pad, brake linings
- Reducer fault: gears, bearings, sealing gaskets, sealing box, reducer
- Electrical fault: motor rotor, bearing, electromagnetic coil, slip ring, carbon brush, collector